Safety Valves
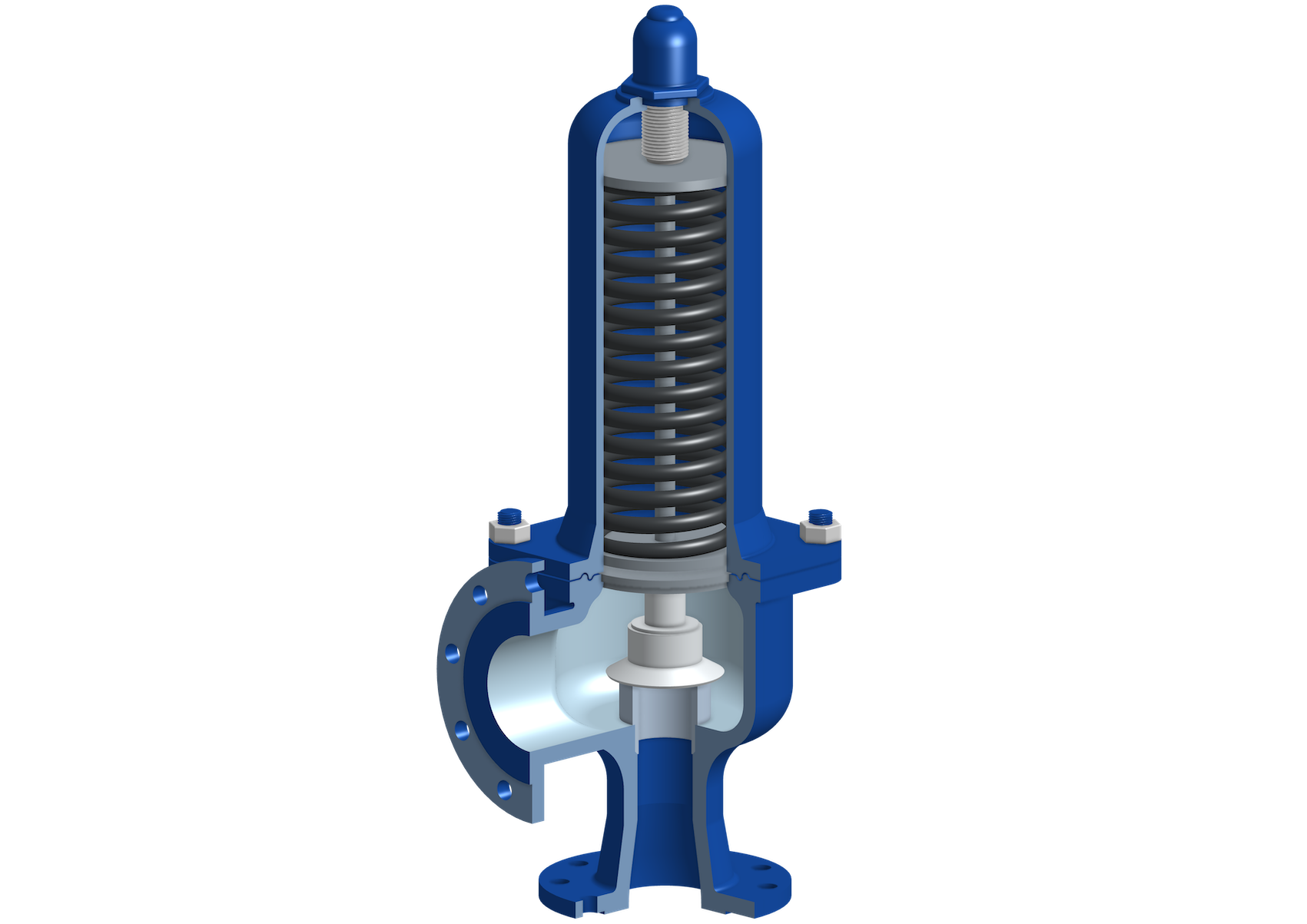
Safety valves are used to protect the components of a plant against high pressure conditions which would exceed their corresponding design pressures. If a certain pressure is reached, the safety valves open to release process medium from the affected process volume in order to prevent a further increase of the pressure. Safety valves are commonly installed at the upper end of the protected process volume so that the hydrostatic pressure needs to be considered when defining the design pressure for components located further below. For the fabrication of safety valves, the conformity assessment procedures according to category IV of the pressure equipment directive 2014/68/EU are applied.
The potential of the medium being in either the gaseous as well as the solid state at the inlet of the safety valve in case of a pressure relief event necessitates the discharge capacity to be determined for both states, as it differs for different densities of the released medium.
Safety valves must only open in the case of upset conditions, meaning that there must be at least one independent mechanism that is meant to prevent the pressure to increase up to the set pressure of the safety valve. The safety valve limits the pressure if this mechanism fails.
Set Pressure and Closing Pressure
The pressure at which a safety valve opens is called the set pressure. In contrast, the pressure at which the safety valve closes again is called the closing pressure. It is important to note that both values refer to the actual pressure difference between the inlet and the outlet side of the safety valve. Not only the pressure within the process volume must therefore be considered, when defining the set pressure, but also the given pressure on the outlet side of the safety valve as well as the dynamic pressure losses via the inlet and outlet pipes occurring in a pressure relief event.
For some types of safety valves, the discharge capacity is a function of the pressure at the inlet of the safety valve. In this case, once the set pressure is reached, a further increase of the pressure within the process volume is required for the safety valve to fully open and to reach its full discharge capacity.
Inlet and Outlet Pipes
In a pressure relief event, when a safety valve is activated, dynamic pressure losses occur via the inlet- and outlet pipes. These pressure losses have an impact on the process conditions at the safety valve and must be considered for the sizing in order to ensure, that the required discharge capacity will be reached.
Excessive dynamic pressure losses via the inlet and outlet pipes can reduce the pressure difference across the safety valve such that it closes prematurely when the pressure inside the process volume is still too high. With the flow interrupted and the dynamic pressure losses gone, the pressure difference across the safety valve rises again, which can cause the safety valve to open anew. This effect can cause the safety valve to open and close in quick succession and to eventually incur damage.